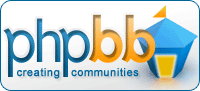 |
The New Generation Of Banging Hardtechno The New Generation Of Banging Hardtechno
|
View previous topic :: View next topic |
Author |
Message |
kinggogof
User HTA
Joined: 28 Apr 2011
Posts: 110
Read: 0 topics
Warns: 0/5 Location: England
|
Posted: Tue 0:32, 24 May 2011 Post subject: gorras ed hardy materials |
|
|
A continuous-mode design of complex parts
Crooked election. 6. Limit column; due to the deep drawing mold process, therefore, must take into account the depth of transfer mode. In the process of transfer mode, if the transfer mode of forming deeper than the height of the forming die is easy to bash. To this end,mulberry outlet, maximum upload bit column in the mold, the punch size limit column as the base level are o (b J t second mold shown in Figure 4. 1. Fixed pitch mode; strips from the first set of dies into the second mold, the use of materials on the shelf section to locate the positioning holes. Since the positioning of this mold from the pin hole of the L can not be finished with the first base line set of dies to be grinding pins, but This increases the positioning hole and the locating pin gap, reduce the positioning accuracy. In punching, the hard to ensure 17; - 'coaxial with the requirements of .1. Therefore, using the four positioning pins, and requires step positioning pin hole consistent with the first set of dies. Thus, the positioning error can be eliminated to ensure the accuracy of the location of the hole. 2. die form; in forming the underside of piercing and flanging. to touch on the emergence of the concave blanking level surface. In order to solve the problem of low surface edge of the grinding, cutting edge part of the low surface made of inserts, embedded in the sub-sag quite. This can be easily removed for sharpening the inserts, and large Au touch and three inserts must be the same amount of sharpening to maintain the relative height between them, without causing material may be suspended under the state in the blanking. 3. small punch guide: Drawing the bottom of the hole 2 . It and the small convex flanging chess Bottom I.1 long thin face, very rigid whole, and the discharge does not pull punches from the two small guide to make it easy to break in the blanking. In view of this situation , embedded in the discharge guide plate inserts,louboutin københavn, they are equipped with a small punch clearance for the double-sided table 0.02 ~ 0.03mm. to protect a small punch. 4. care feeding device: In the bending process, the Taking into account part of the rebound of the cavity surface grinding bending angle of a bounce,mac cosmetics discount, but Andrew made the parts in the package tightly after bending die, and difficult to remove. We care die coat the feeding device, which consists of care expected short, composed of hard rubber and screws, such as Kids in 5. bending, by a hard rubber material to prop up the block from the top, you can put the top part out, care expected size of the force adjusted by the screws 5.. unloaded pour plate assembly Methods: In the past four 10-mode is used the total county industrial 1989.No.1 95 Figure 5 - 6 Kids in the discharge screw pull pull, unloading unloading debate debate panel by a screw adjustment rubber elastic, but not easy to manually adjust the uniform, which led to the discharge board skew, resulting in knife-edge blanking is the phenomenon of eating, and even the small convex See all broken. t us to improve this measure, that is; with washers, bushings and cylinder head screws to form a group, instead of screws,mulberry väskor, as shown in Figure 6. As the grinding together of four of its end bush, so they are exactly the same height, this set of four lining punch in the stripper plate and between the fixed plate, and through the Cylinder head gasket with screws hold the stripper plate. so, it will be leveled stripper plate, stretch the rubber on its distribution, thus One} to suppress the strip, and better protection of the punch. Chong hole cutting corners expected modulus of continuity Optical Instrument Factory, Changde City, South China Yang Jian Figure 1 is a fan on my factory production parts, materials, 10 steel, the thickness of 1mm, 'large quantities. This typical parts stamping process is generally used composite modulus or the modulus of continuity for the traditional, such as composite blanking die, punch and die wall thickness of the red parts by size constraints, the data obtained by the data check shows that its minimum thickness punch has been in critical condition, so it effects of manufacturing process more sensitive to punch strength is not well guaranteed. If the traditional side of the blade fixed pitch die, although the strength to solve the mold problem, but the additional waste material caused by the traditional low} If no Figure 2 Modulus of punching waste, its main problem is prone to dislocation wide access pox, burr, so that the amount of red parts Ba severely affected, and burr is often caused by the accident risk. Figure 3 is designed punching shear as shown in the corner without waste materials die, she rushed out of the parts successfully. Xia J The blanking process is as follows (see Figure 3): first strip against the guide block 7, to send overflow,gorras ed hardy, by visual inspection to drag strip ends into his corner cutting die cavity l ~ 2mm. in the first place by a process step 2 punch punch punch, and punch a corner cutting head trimming materials to control subjects admitted to bar distance. To ensure that the die strength, the second process step based juice into space. Stock to continue feeding close to the positioning block 4, in the third position on the process step by the cutting angle convex die angle separation. cut down the angle to stay in the concave mold, was sent to the strips behind the push to go, falling into the concave die staring at the back of the hole angle and drain away from the hole. Results from the simplified mold out hair, not set off the initial block material, so every All roads of the first workpiece material is not out of the hole in the process waste. Figure 2 chess with the total 95 industrial 1989.N0.1
相关的主题文章:
Mulberry tasker rapid prototyping
christian louboutin select a combination of push tube and push the program
ed hardy zürich see Figure 1
The post has been approved 0 times
|
|
Back to top |
|
 |
|
 |
|
|
You can post new topics in this forum You can reply to topics in this forum You cannot edit your posts in this forum You cannot delete your posts in this forum You cannot vote in polls in this forum
|
fora.pl - załóż własne forum dyskusyjne za darmo
Powered by phpBB © 2001, 2005 phpBB Group
|