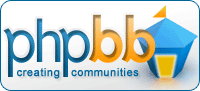 |
The New Generation Of Banging Hardtechno The New Generation Of Banging Hardtechno
|
View previous topic :: View next topic |
Author |
Message |
qplmw719
beginning to like HTA
Joined: 23 Dec 2010
Posts: 81
Read: 0 topics
Warns: 0/5 Location: England
|
Posted: Thu 2:48, 20 Jan 2011 Post subject: air max 2009 Nike Tiempo Legend III AG iD (Wide) W |
|
|
Nike Tiempo Legend III iD CleatStart simple and go from there. With its traditional silhouette in supple kangaroo leather intact,[link widoczny dla zalogowanych], the Nike Tiempo Legend III iD stakes new territory. The choice of the game?s top players has moved beyond mere expectations,[link widoczny dla zalogowanych], re-engineered into a cleat of wonder. With a focus on fit, as well as plate options, this cleat supports all moves with unbelievable grace, finesse and power. Like a perfectly-pitched piano,[link widoczny dla zalogowanych], the Legend III is tuned and ready to perform. Futbol maestro, please. Premium kangaroo leather upper for superior comfort and control during ball strikeAvailable in Men?s and Women?s sizes with regular and wide fit optionsChoice of four outsole plate options: firm-ground (FG), soft-ground (SG), artificial grass (AG), hard-ground (HG) Formed heel for improved comfortMolded sockliner with PORON
The post has been approved 0 times
|
|
Back to top |
|
 |
|
 |
View previous topic :: View next topic |
Author |
Message |
op91oppu
beginning to like HTA
Joined: 16 Feb 2011
Posts: 57
Read: 0 topics
Warns: 0/5 Location: England
|
Posted: Thu 11:00, 24 Feb 2011 Post subject: |
|
|
Delivered to your door >>
Renew Your Subscription >>
Relationship of Torque and Shaft Size Written by Chuck Yung and Cyndi Nyberg, EASA Article Index Relationship of Torque and Shaft Size page 2 All Pages
Pumps & System, June 2008
Bigger Is Better-Or At Least It Used To Be
Owing partly to tradition, the shafts of electric motors are often larger than those of the equipment they drive. Engineers were very conservative a century ago when electric motors first came into widespread industrial use, so they typically designed in a sizable margin of error. Today's engineers haven't changed much in this respect. For example, standard NEMA frame dimensions, which have been revised only once since 1950, still specify much larger shaft sizes than commonly accepted principles of mechanical engineering would require.
Shaft Design Basics
Shaft size is dictated by torque, not horsepower, but changes in horsepower and speed (RPM) affect torque, as the following equation shows:
Torque (in pound-feet) = HP x 5252/RPM
Accordingly, an increase in horsepower would require more torque, as would a decrease in rpm. For example, a 100-hp motor designed for 900-rpm would require twice as much torque as a 100-hp motor designed for 1,800-rpm. Each shaft must be sized for the torsional load it is expected to carry.
Two basic, quite conservative approaches are used to determine the required minimum shaft size for motors. One method calls for making the shaft large enough (and therefore strong enough) to drive the specified load without breaking, defined by mechanical engineers as the ability to transmit the required torque without exceeding the maximum allowable torsional
shearing stress of the shaft material. In practice, this usually means that the minimum shaft diameter can withstand at least two times the rated torque of the motor.
Another way to design a shaft is to calculate the minimum diameter needed to prevent torsional deflection (twisting) during service, meaning for engineers that the allowable twisting moment, or torque, is a function of the allowable torsional shearing stress (in PSI or kPa) and the polar section modulus (a function of the cross-sectional area of the shaft).
Machinery's Handbook provides the following equations for determining minimum shaft sizes using both design approaches: resistance of torsional deflection and transmission of torque. Both sets of equations are based on standard values for steel, with allowable stresses of 4,000-psi (2.86-kg/mm2) for power-transmitting shafts, and 6,000-psi (4.29-kg/mm2) for line-shafts with sheaves (the proper name for what most of us incorrectly call pulleys). Some of the equations are also specific to keyed or non-keyed shafts-handy for pump users who need to know how to calculate the size of each kind.
The Transmission Of Torque Approach
Most motor shafts are keyed,steel shaft, which increases the shear stress exerted on the shaft. Considering this, motor shaft designs typically use no more than 75 percent of the maximum recommended stress for a non-keyed shaft, which is also why electric motor shafts are often larger than the pump shafts they drive.
Example 1
Consider a 200-hp (150-kW), 1,800-rpm motor. For a direct-couple application, the standard frame size is 445TS, with a (keyed) shaft diameter of 2.375-in (60-mm). Using Equation [1], the minimum shaft size would be:
Since the calculated shaft diameter for a 200-hp motor is designed to withstand twice the rated torque, the shaft diameter of 2.371-in is at the absolute minimum for the 400-hp rating.
Resistance To Twisting Method
The other way to calculate minimum shaft size for a motor is to set a limit on the amount of torsional deflection (twisting) that may occur. Resistance to torsional stress is directly proportional to shaft size: the larger the diameter, the greater the resistance to twisting.
A rule of thumb with this method is that the shaft must be large enough that it will not deflect more than 1 degree in a length of 20 times its diameter. To calculate the minimum shaft size to meet this specification, use the following equation:
Example 2
For the 200-hp (150-kW), 1,800-rpm motor from Example 1, the minimum shaft size to limit torsional deflection would be:
The minimum shaft diameters calculated by the torque transmission and torsional deflection methods are essentially the same for Examples 1 and 2. Still, a good approach is to calculate the size both ways, and then use the larger value as the absolute minimum.
Hollow-Shaft Designs
Direct-coupled loads exert a twisting force (torsion) on the shaft, placing the greatest strain near the surface or radius and very little on the inside portion, which makes hollow-shaft designs practical for vertical motors. These designs allow the pump shaft to pass through the hollow motor shaft, which simplifies the coupling process for pump shafts that must support the heavy water column associated with a deep well.
The calculations for shaft diameter are not quite as straightforward for a vertical hollow-shaft motor. Two variables-the outside and inside diameters of the hollow-shaft-are not standardized, making it impossible to simplify the calculation with a ratio. For this reason, it is easier to demonstrate if a specific hollow-shaft is sufficient for a given power rating.
The post has been approved 0 times
|
|
Back to top |
|
 |
|
|
You can post new topics in this forum You can reply to topics in this forum You cannot edit your posts in this forum You cannot delete your posts in this forum You cannot vote in polls in this forum
|
fora.pl - załóż własne forum dyskusyjne za darmo
Powered by phpBB © 2001, 2005 phpBB Group
|