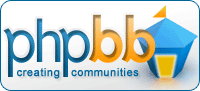 |
The New Generation Of Banging Hardtechno The New Generation Of Banging Hardtechno
|
View previous topic :: View next topic |
Author |
Message |
tammi7r1b4d
Newbie
Joined: 03 Apr 2011
Posts: 35
Read: 0 topics
Warns: 0/5 Location: England
|
Posted: Wed 10:49, 13 Apr 2011 Post subject: jordan 11 grey Art of Native American Flute Making |
|
|
Cutting and Routing
John fashions a long semi-circle groove down each half of the flute with a cove bit. When the flute's halves are rejoined, these grooves will create the hollow inner parts of the instrument: the bore and slow air chamber. Routing the groove requires at least three passes. He flattens any warping and sands the edges. This removes a fraction of wood, so John must return to the router to regain the precise depth. At this point, John tapers the mouth end of the inner cavity to fashion the mouth hole.
At first, John found flute making far more complicated than he’d anticipated. He admits his first flutes were humble instruments, but with each attempt, his understanding of flute dynamics improved. He received help and encouragement from other flute makers, and in time the sound and appearance of his instruments grew stunningly superb.
Read on
Christmas Carol Native American Flute Music Tabs
Best Gift Ideas to Buy for a Music Lover
How To Improvise Native American Flute Music
Crafting the Mouth Piece, Plug [link widoczny dla zalogowanych], and Sound Hole
Next, John deftly cuts the true sound hole and exit of the slow air chamber. He sands the inside of the flute and brushes it with sealant.
Beginnings of a Flute Maker
John Stillwell's Native American flutes aren’t only captivating to the ear; the instruments are crafted with colors, patterns, and shapes stimulating to the eye as well.
For ten years, John has fine-tuned his art. “For me,” he writes, “craftsmanship involves the constant seeking after perfection. There is an ideal sound calling from just over the horizon. It calls from a place just beyond the best flute I have ever made. Striving for this ideal makes me focus on even the most minute detail that affects the flute’s sound. I have an obligation to bring that Spirit to every flute I make, because the flute player deserves no less.”
John Stillwell first picked up a river cane flute at a swap meet. “I didn’t even know the instrument was called a Native American flute,” he reminisces. “A vender was asking $15 for his flutes [link widoczny dla zalogowanych], but he had this flimsy, crooked flute for $7. I wasn't sure whether I’d be able to play it or not, so I took the crooked one. Lo and behold, I started to make interesting, satisfying music without a great deal of effort.”
With 25 years of woodworking experience, John quickly progressed from a player to a maker of the Native American flute. “I gravitated toward better and better instruments,” he remembers, “Finally, I realized the instruments I wanted were $300, so I thought I ought to be able to make them for myself.”
When the instrument is dry [link widoczny dla zalogowanych], John removes it from the press and scrapes away excess glue. Next, he flattens the bottom side of the flute on the belt sander and ru
John begins the painstaking process of roughing out a flute by selecting his wood, discarding any with knots or cracks, and cross cuting boards to the approximate length of a finished flute. He checks for exact thickness then rip cuts each flute-shaped block with the table saw to divide it longways . When he rejoins the two halves , the grain will match perfectly down the flute’s center.
The next step is making a plug to separate the bore from the slow air chamber. John cross cuts a birch dowel to craft a piece with one end slanted at ninety degrees and the other at 52-degrees. After the plug is cut, he sands and soaks it in polyurethane.
John spreads glue along the edges into an even film with his finger. Finally, he positions the plug and joins the halves together. He swabs excess glue with a damp cloth while the instrument dries in a press.
The post has been approved 0 times
|
|
Back to top |
|
 |
|
 |
|
|
You can post new topics in this forum You can reply to topics in this forum You cannot edit your posts in this forum You cannot delete your posts in this forum You cannot vote in polls in this forum
|
fora.pl - załóż własne forum dyskusyjne za darmo
Powered by phpBB © 2001, 2005 phpBB Group
|